Hydrogen internal combustion engines (ICEs) are a promising alternative to conventional carbon-fueled engines in a diversified global energy transition. Hydrogen ICEs can be advantageous due to their potential to produce zero carbon emissions during operation. However, to reduce NOx emissions due to high combustion temperatures, hydrogen must be burned lean or under dilute conditions, which increases the potential for cyclic variations due to unpredictable hydrodynamic and thermodiffusive instabilities. Therefore, a better understanding of the complex interaction between engine flows and combustion dynamics of lean or dilute hydrogen is required to design efficient and effective hydrogen-fueled engines. To achieve this goal, flow velocities, ignition characteristics, flame visualization, and mixture formation are characterized using laser diagnostics in an optically accessible single-cylinder research engine.
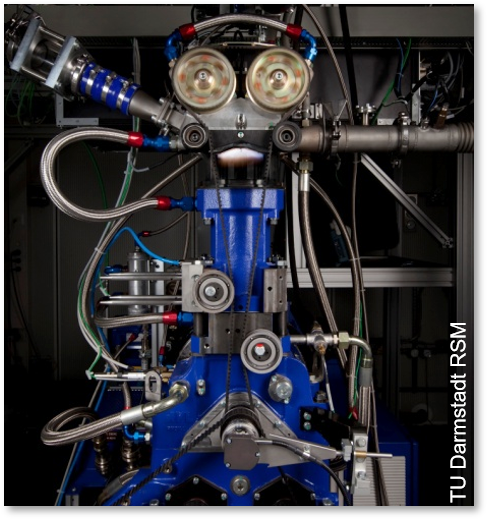
Figure 1. Darmstadt engine test bench
An optically accessible spark-ignition (SI) engine with port fuel hydrogen injection is used for this investigation. The engine test bench at the Institute of Reactive Flows and Diagnostics at TU Darmstadt, shown in Figure 1, is employed to provide consistent and well-controlled boundary conditions for the investigation of the phenomena involved and to support the development of a validation database. Lean or diluted (via exhaust gas recirculation) hydrogen-air mixtures are provided by a gas mixing system and a series of mass flow controllers to allow precise control of the operating conditions. The turbulent flow field is characterized by particle image velocimetry (PIV) before and during early flame development. In addition, flame propagation is simultaneously captured by laser-induced fluorescence (LIF). Figure 2 shows an example of simultaneous flow and flame imaging measurements acquired in the Darmstadt engine which have been used to study the correlation between the flow field and cyclic combustion performance [1].
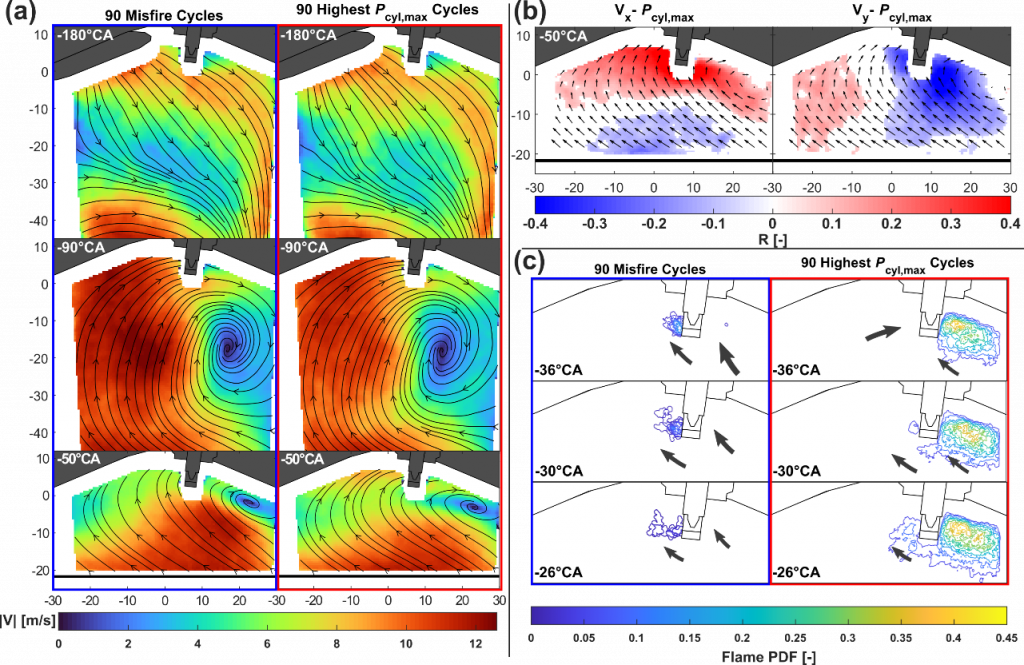
Figure 2 (a): Conditioned phase-averaged flow fields separated by 90 misfire cycles and 90 cycles with the highest maximum in-cylinder pressure for 14.% EGR at 1500 rpm and with 0.4 bar intake pressure. (b): Correlation field for the x and y components of velocity and the maximum in-cylinder pressure over 805 cycles. (c): Flame-flow model comparing the conditioned misfire and high maximum in-cylinder pressure cycles. Figure reproduced from [1].
This research project consists of three main parts: (1) Investigation of local flame dynamics under real ICE conditions, (2) Investigation of cyclic variations at high EGR rates in part-load operation, and (3) Provision of experimental data for modeling and validation. By completing all three parts, the cause-and-effect chain governing combustion instabilities in hydrogen engines will be elucidated.
References
- C. Welch, M. Schmidt, L. Illmann, A. Dreizler, B. Böhm: The Influence of Flow on Cycle‑to‑Cycle Variations in a Spark‑Ignition Engine: A Parametric Investigation of Increasing Exhaust Gas Recirculation Levels. Flow, Turbulence and Combustion 110: 185-208 (2023). https://doi.org/10.1007/s10494-022-00347-5
Contact:
Dr.-Ing. Benjamin Böhm boehm(at)rsm.tu-darmstadt.de
Prof. Dr. habil. Andreas Dreizler dreizler(at)rsm.tu-darmstadt.de
Cooper Welch welch(at)rsm.tu-darmstadt.de