This project focuses on numerically investigating the impact of cycle-to-cycle variations of anomalous combustion phenomena and analyzing the underlying processes. Due to hydrogen’s intricate auto-ignition characteristics and pronounced differential diffusion, modeling and simulation pose additional challenges. Auto-ignition events can occur before spark ignition (pre-ignition) or after the primary combustion phase (knocking). Both engine-relevant anomalous combustion phenomena will be analyzed by systematically considering local and global influencing factors under engine operating conditions.
Initial investigation of auto-ignition will involve generic flame configurations, initially without turbulence effects. The interaction between auto-ignition kinetics, differential diffusion, and strain/inhomogeneity effects will be explored. Validation and application of the auto-ignition model will progress through systems of increasing complexity. Validation under turbulent conditions and temperature inhomogeneities will be done using Direct Numerical Simulation (DNS) data from TP 2. The adapted modeling will then be applied to experiments of auto-ignition of premixed hydrogen-air mixtures at temperature-controlled surfaces in a high-pressure chamber (TP 6). Here, the setup allows the study of isolated factors’ effects.
Building upon this, the occurrence of anomalous combustion phenomena in engine operation will be investigated, particularly the impact of inherent cycle-to-cycle variations. The extended auto-ignition modeling enables multi-cycle Large Eddy Simulations (LES), considering temperature and mixture inhomogeneities. The engine-based investigation expands on the high-pressure chamber setup, studying the interaction of auto-ignition with small- and large-scale variations in flow motion, residual gas distribution, and previous cycle effects.
Finally, a backward cause-and-effect chain analysis is conducted in close collaboration with TP 6, employing single-cycle analysis in simulation and experiments.
In summary, the project comprises of three main objectives:
- Model development for describing hydrogen-air mixture auto-ignition under inhomogeneous conditions (temperature, mixture).
- Application and validation of an auto-ignition model in LES configurations, including experiments on surface-induced auto-ignition and selected engine operating points.
- Identification and evaluation of factors influencing anomalous combustion phenomena during engine operation, achieved by analyzing auto-ignition results and considering cycle-to-cycle variations.
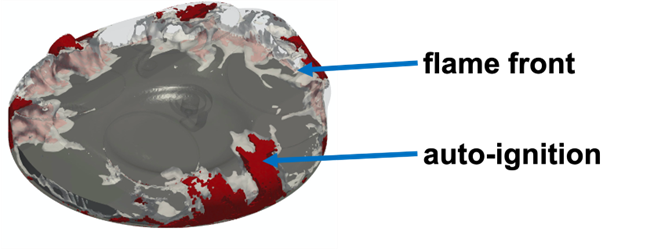
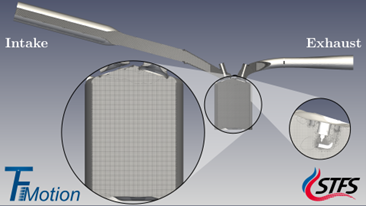
Contact:
Prof. Dr.-Ing. Christian Hasse hasse(at)stfs.tu-darmstadt.de
Magnus Kircher kircher(at)stfs.tu-darmstadt.de
Tim Jeremy Patrick Karpowski karpowski(at)stfs.tu-darmstadt.de